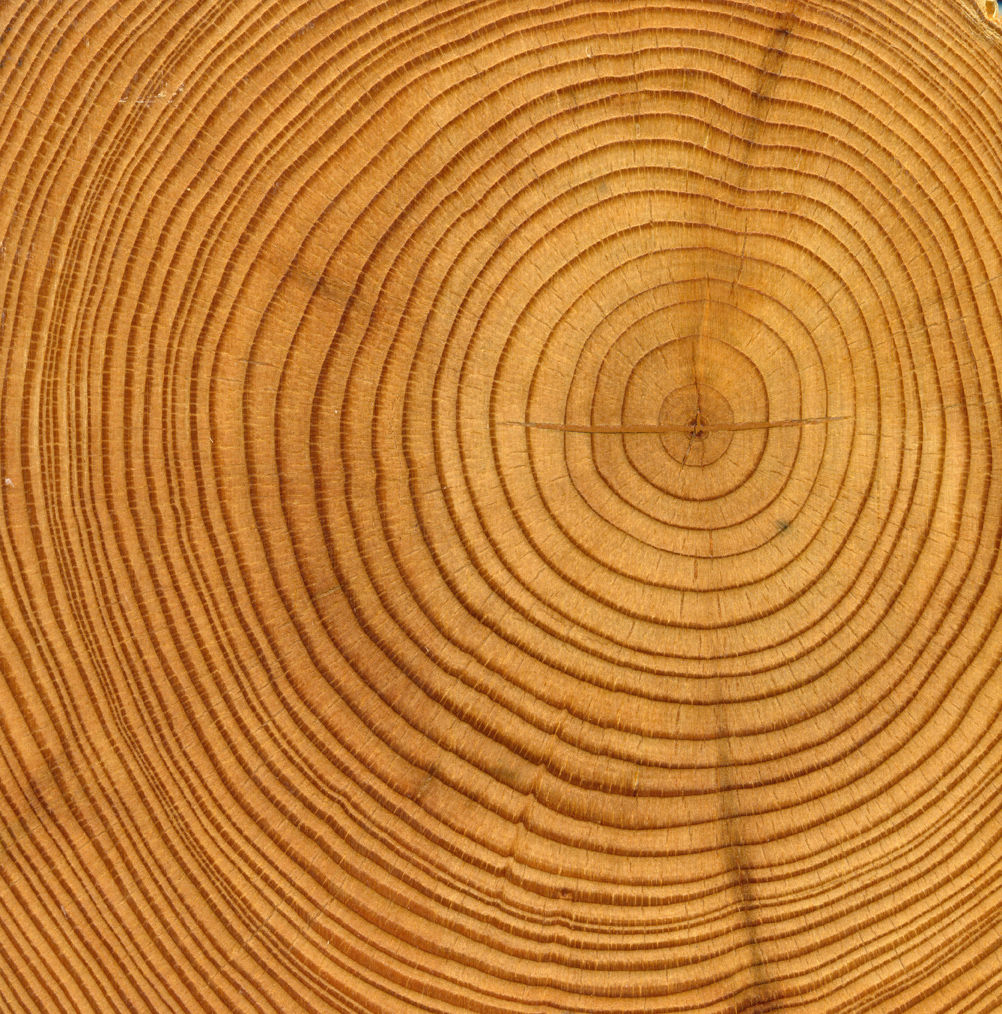
KNOW
YOUR
WOOD
Considering our long-term environmental influence, the usage of wood is very important as it is a natural, renewable raw material.
Wood also serves as a beautiful decorative material - a wide scale of decorations can be created by mixing details from different kinds of wood, coatings and technologies.
Furthermore, wood possesses even more remarkable features which in many ways give it a leading position over alternative materials:
excellent heat and sound insulation independent of the temperature, as well as the fact that wood does not accumulate electrostatic charges are a few examples.
One of the features of wood is to exchange moisture with the surrounding air, which helps to keep a balanced humidity in a room with wooden windows. Under stable humidity surroundings the wood helps keep its moisture in balance. The correlation between the relative air humidity and the wood moisture is shown in the enclosed chart. By increasing or decreasing the humidity, the wood starts to swell or shrink accordingly.
Moisture causes the wood to swell minimally along the fibres, more sufficiently across them and mostly along its tangential cut. Swelling and shrinking can differ depending on the kind of wood.
Cycled or even single swelling or shrinking of the wood surface may cause severe damage to the treated surface resulting mostly in cracking which appear on the surface of the coating.
To minimise or to avoid the risk for cracking, wood with the proper moisture content should be used. The wood moisture should be kept stable during the treatment process as well as during storage, transportation and usage.
According to the opinion of many specialists, the recommended moisture content in wood to be used for indoor furniture should be 6-8%, and for windows and outer doors 12-15%.
Some properties are in common in every kind of wood: year-rings, resin, knots, pores, etc.:
In the wood cells, which are the building bricks of the tree, the cells of the spring wood have thick walls and a large cavity; the summer wood cells however have thicker walls and smaller, flatter cavities.
The summer wood is a harder, denser material than that of the spring wood.
Some kinds of soft woods, the so called fat kinds of wood, are characterized by more or less resin contents whilst the hardwoods often have big cell rooms or pores. Resin, or sapwood, are often present in the outer year-rings which are paler while the heartwood, the inner rings, is normally darker.
Different kinds of heartwoods are pine, larch, oak, yew-tree, ash, elm, willow, poplar, mountain ash, walnut etc. Birch is an example of wood without heartwood.
Year-rings are formed by the tree’s yearly growth and consist of two bands: a light-coloured band which is directed towards the tree centre and a darker band directed towards the bark.
The inner band of the ring is formed at the beginning of the cambium growth and is therefore called “Early wood.” The darker outer band grows at the end of the summer and is therefore called “late wood.”
Ash, mahogany and coto are examples of hardwood with bigger pores, and these can cause blisters when they are coated – this is a well-known phenomenon.
The natural “yellowing” which occurs under the influence of UV-light contained in solar radiation is typical for soft wood.
This process of “yellowing” can be significantly retarded or eliminated by using special UV-resistant lacquers. Certain sorts of soft wood contain large amounts of resin, which might result in the occurrence of grey spots during the treatment of such wood.
For this reason, the drying process of the coated soft wood should not be done at higher temperatures as the resin starts to dissolve at +45° C.
SOFT WOOD
HARDWOOD
There are two types of surface treatment for hardwood: open- and closed-pored.
In the former the coating fills up the pores, and in the latter it only covers the surface.
BOARD MATERIALS
A large number of wood-based board materials are used in the production of furniture and interior decorations.
The most predominant materials are chipboards, MDF-boards and hardboards.
The different kinds of board have different characteristics regarding density, evenness, moisture resistance etc.
CHIP BOARDS
Chipboards are manufactured by hot pressing of resinous wood chips. Chipboards can have different thicknesses, densities, and usages depending on the refinement.
Some examples are: fine layer-boards, chipboards with coated paper, foils or melanin and chipboards with fillers.
Chipboards are used for the production of wardrobes, bookshelves, beds and walls. It
has lately become possible to achieve a significant reduction
of formaldehyde emissions in chipboards by using new adhesives.
FIBREBOARDS
Fibreboards are manufactured by hot pressing of wooden fibres. Compared to chipboards, the surface of a fibreboard is much easier to treat.
Fibreboards are used for manufacturing different kinds of board components in furniture production. The most popular boards are MDF-boards (medium density boards) and HDF-boards (high density boards).
In the manufacture of high density boards the so-called “wet process” is used whereby the shaping of a board is done at high temperatures and under high pressure. The adhesion between the fibres is achieved mainly by the natural resins contained in wood, yet artificial resins might also be used.
For manufacturing medium density boards the so-called “dry process” is used involving a lower temperature and lower pressure.
Adhesion between the fibres is done by synthetic resins. MDF-boards are manufactured in different thicknesses, densities and surface treatments. MDF-boards with special features, such as resistance to moisture, fire, weather conditions or with a higher density are also widely-used.
The usage of MDF-boards has increased and practically replaced massive wood as a raw material when top coating (e.g. turned and profiled objects).
VENEER
Veneer is manufactured from slicing or turning and is normally 0,5 – 0,8 mm thick. When producing veneer, breaches in the material easily occur, and this can later on be seen as cracks in the veneer and the lacquer layer.
Veneer is normally used in the production of furniture and interior decoration details.
It is often used in the production of high-quality details; and for this reason the demands on the veneer coating are very high regarding elasticity, adhesion etc; the choice of surface treatment system is also very important.