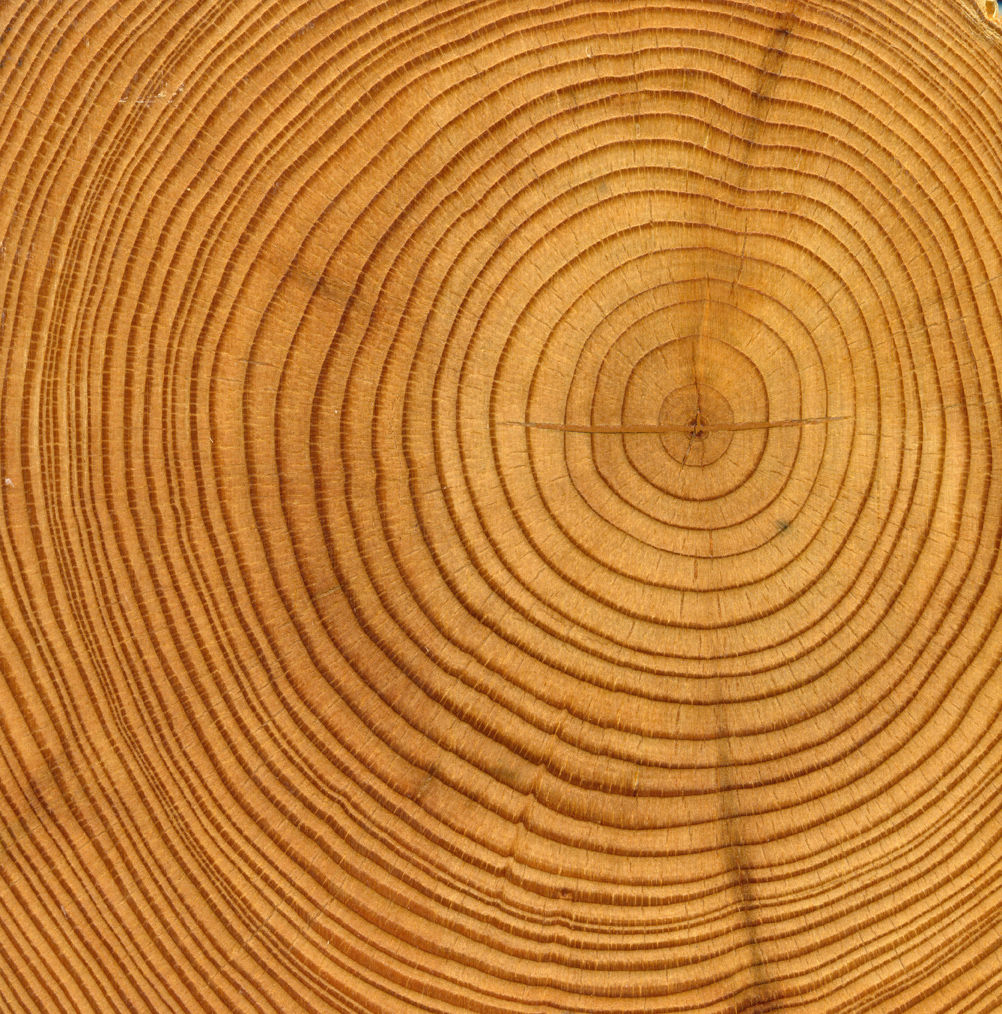
SANDING
-
to calibrate the objects to the required size;
-
to remove scratches, splinters, pencil marks, glue residues and other defects from the surface;
-
to remove grain raised from the surface by moisture or coating;
-
to assure adhesion between the coating and the surface, or between coats;
-
to reduce the consumption of coating material, as improperly sanded wooden surfaces absorb the coating and grain raising more intensively;
-
to produce a good end-result with the correct sanding technology & surface treatment material;
-
to emphasize the natural beauty of wood and its structure;
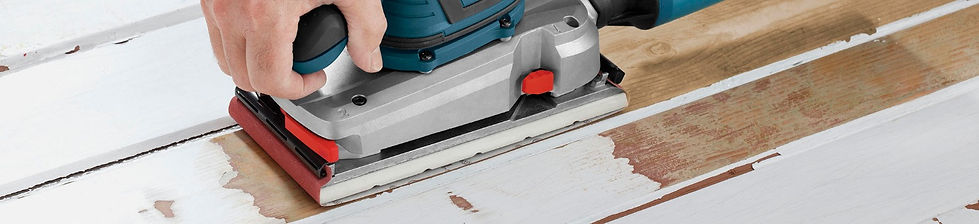
SANDING MATERIALS
A sanding belt consists of a basis (paper, fabric or a combination of both) onto which the abrasive grains are stuck using an adhesive. Normally belts used for higher tension have a mixed and firm basis. Belts for sanding profiled surfaces are made from an elastic fabric basis.
Both natural and artificial subjects are used as abrasive materials. Artificial abrasive materials are harder and their usage is more extensive.
The choice of grains for different abrasive materials depends on the purpose of a sanding belt. The most commonly used abrasive materials are the oxides of aluminium (corundum), zirconium and silicon carbide.
The abrasive materials are divided into ten grades of hardness (Mohs’ scale); the hardness of the tenth grade equals diamond hardness.
Abrasive grains are primarily diminished and then sorted in fractions by straining. The grain’s fraction size is determined by the number of holes in one square inch of a sieve and is defined by rounded numbers (40, 60, 80, 100, 120, 150, 180 etc). The bigger the number - the more holes per square inch of the sieve, thus the smaller the grains are.
Paper-based materials are sorted in accordance with the paper density as follows: A-paper (60-80 g/m²), B-paper (95-105 g/m²), C-paper (114-126 g/m²), D-paper (146-158 g/m²), and E-paper (218-242 g/m²).
Abrasive grains may be spread over the basis in a tight (close coat) or loose (open coat) way. Sandpaper with loosely applied abrasives should be used for sanding the resinous kinds of wood (pines, dens).
There are not only belts, but also other special materials used for sanding, wool or felt made of abrasive fabric, sanding brushes, sanding sponges etc.
Sanding is an important technical stage of the surface treatment process. The sanding has the following aims:

SANDING RECOMMENDATIONS
The sanding should be done without any extreme tension of the belt. Too high a tension results in a belt’s premature wear and loss of finishing quality of a treated object. An optimal tension of the sanding belt significantly increases the belt’s life-time, improves the quality and reduces consumption of the coating material.
The usage of a flexible press during the sanding preserves the sanding belt and improves the sanding quality significantly.
It is necessary to check the direction of a sanding belt when placing it on the roller of a sander. The correct direction is indicated by an arrow drawn on the reverse side of the sanding belt.
The tension of a sanding belt should be reduced after the end of a sanding
process in order to avoid stretching the belt and to prolong the belt’s life-time.
The speed of the sanding belt and feeder should be set in accordance with the properties of the treated surface and recommendations of the belt manufacturer.
During operation of a sanding unit, all contact between a sanding belt and metals or other firm materials should be avoided as it may result in a break or destruction of the grains of the sanding paper.
It is necessary to make regular checks of the dust-disposal system and to constantly ensure a clean working environment.
The usage of the proper sanding materials improves the sanding results.
It is not recommended to go into a finer sanding by changing the size of the grains too much during some sequential sanding cycles. For such cases the usage of materials with the following range can be recommended: 60-100-150-220 or 40-80-120-180-240.
The quality of the surface will be much better on a finely sanded wood object if it is sanded with grains of size 180 instead of 120, which gives a heavy grain raising that binds the primer on top of the surface.
Grains of size 180 give less grain raising, thus the primer will penetrate the wood surface better and doesn’t have to be sanded away.
For this reason, the final wood sanding should be done with a sanding paper with fine grains. If the sanding furthermore takes place immediately before the priming, the adhesion will be much better.
SANDING EQUIPMENT
The most popular sanding machines used for sanding along the fibres are the wide-belt sanders (with a roller or a so-called pad contact).
For sanding across the fibres use narrow-belt sanders, vibration belt sanders, circle sanders for example.
Sanders with special structures are used for sanding edges and profiles.
It is often possible to combine different ways of sanding
in order to achieve better results.
