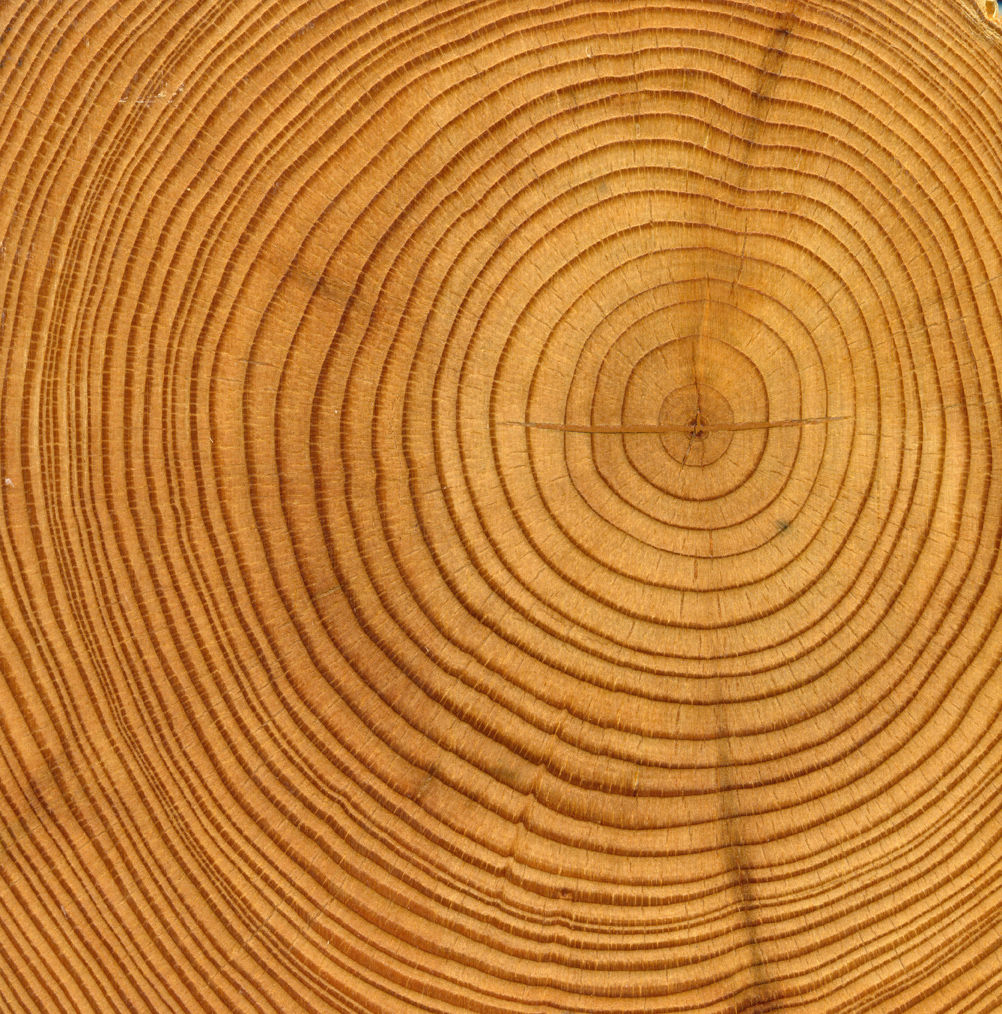
SPRAYING

SPRAYING ROOMS
Spraying rooms should be used to improve the spraying results. The rooms also serve to ensure a cleaner working environment by removing solvent vapours and spraying particles from the coating. Depending on the type of applied filter, there are spraying rooms with dry, wet and mixed filters. Constant airflow coupled with good ventilation is of great importance.
To ensure a good coating quality, the incoming air must be pre-filtered to eliminate dust particles and must be warmed up in the cold season.
In the rooms where a dry filter is installed, the remainders of the finishes are removed by a glass-fibre filter or by a paper filter. The effectiveness of removing finishes from the spraying room by such a filter is 70-90% with a ventilated air flow speed of approximately 0,5 m/sec. Spraying rooms with dry filters are mostly used in small production areas.
In spraying rooms with hydro filters, the coating residues are eliminated by using water.
Coagulants are combined with water to sink the residues or to bring them up to the water surface.
The coagulants are chosen depending on the applied coating. In the production process coagulants have to be added according to the consumed amount of coatings to enrich the solvent. Both the room and the water containers have to be thoroughly cleaned afterwards.
Conventional air spraying is the most flexible and adaptable method whereby the coating is sprayed through a gun nozzle using compressed air at 3-6 bars’ pressure.
The coating material is fed forward to the nozzle from the upper lacquer container under gravitational force, or is sucked from the bottom container under high pressure or low pressure. Alternative feeding methods use a membrane pump or pressure vessel.
The amount of coating can be regulated by the supply of compressed air. The advantages of this method are: uniform coating, possibility to use different coating materials, good quality, uncomplicated regulation of the spray width and material consumption.
The disadvantages of this method are: low production rate, fairly high solvent consumption (as it is necessary to use coatings with relatively low viscosity) and significant waste of material during spraying.
CONVENTIONAL AIR SPRAYING

MIXED SPRAYING (AIR MIX)
Air mix is a combination of high pressure and low pressure spraying. The coating material is fed to the nozzle under a pressure which is lower than average (in the range 20-120 bars). The compressed air pressure added for adjustment of the spray width is not higher than 1,5 bars.
Spraying with this type is a compromise which combines the advantages of high pressure and low pressure spraying. This is the most widely-used method for high-quality coatings of wooden surfaces.

HIGH PRESSURE SPRAYING
Spraying under high pressure is done by a high pressure pump which carries the pressure over to the coating. Spraying takes place through the nozzle under a pressure of 90-360 bars.
The spray width can be adjusted by replacement of the nozzle of the sprayer. The advantages of this method are: high production rate, possibility to use coating materials with higher viscosity, reduced waste of spraying material and a possibility to a thicker spray coat than in the case of low pressure spraying.
The disadvantages of the method are: adjustment of the spray width which can be achieved only by replacement of the nozzle and a fairly low coating quality compared to the previous method.

LOW PRESSURE SPRAYING
Low pressure spraying is a modification of conventional air spraying which uses compressed air leaving the spraying gun under a pressure not higher than 0,7 bars. The coating is fed forward to the nozzle in case the upper lacquer container is used under gravitational force, or through the tube of a membrane pump or pressure vessel. The spray width is adjusted by compressed air.
The advantages of this method are: uniform coating at lower pressure, possibility to use different coating materials, good quality, uncomplicated regulation of the nozzle and material consumption and good coating economy compared to conventional air spraying. The disadvantages of this method are: lower production rate and fairly higher solvent consumption.
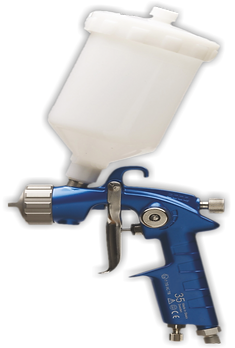
ELECTROSTATIC FIELD SPRAYING
Spraying in electrostatic fields is based on the movement of atomised particles along the power lines of an electromagnetic field which is created between a negatively charged spray gun and a grounded object. The stronger the electromagnetic field between the spray gun and treated object is, the stronger the effect of electrostatic spraying will be. The field power depends on the distance between the spray gun and the treated object, as well as on the potential difference (voltage). Usually the voltage between the earthed object and a spray gun is about 80 kV.
The distance depends on the equipment and might range between 0,3-0,5 m. Apart from the low pressure and mixed sprayer the so-called bell system is used for electrostatic spraying. The working principle of an electrostatic bell system is that the coating, which is led to the high-speed rotary bell, is atomised by centrifugal force at the bell’s edge into small particles that are forced onto the treated objects by an electromagnetic field.
Considering that wooden surfaces have poor conductivity, its moisture ratio should be 10-12% with a relative humidity of the ambient air of not less than 60 - 70% in order to reach the required electrostatic effect. The major hazards of electrostatic spraying are: risk of explosion and risk of electric shock for the
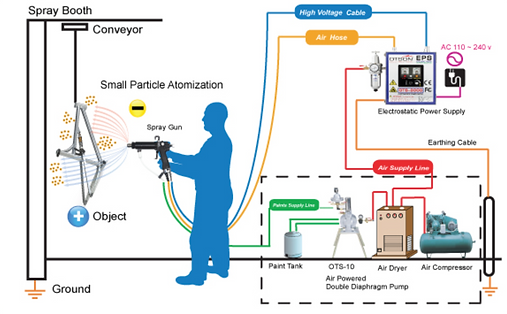
HOT SPRAYING
For hot spraying it is important that the viscosity of the coating is low enough. A solvent is usually added to the coating to decrease the viscosity. Another possibility to decrease the viscosity is to increase the temperature of coating material.
By using hot spraying, a temperature increase of up to 40-80° C takes place inside a special heating unit. Hot spraying allows the solvent consumption to be reduced, which results in a reduction of the drying time, avoiding surplus material, increase of production rate and improvement of the coating quality.
user. In order to avoid the explosion risk, both thetreated objects and the spraying equipment must to be properly earthed in order to eliminate the electric discharge through ignition. Furthermore the flash point of coating has to be fairly high.
The advantages of electrostatic spraying are: extremely small waste of coating material, a high production rate and a uniform coating. The disadvantages are: a rather complicated treatment of inner corners and high installation costs.
TWO-COMPONENTS SPRAYING
This method is mainly used when spraying two-component coatings with a short pot-life. In this application process the base and the hardener are combined in a special pump immediately before spraying. The advantages of this method are: precise and uniform dosage of the applied mixture and a possibility to reduce the costs as the required quantity of applied mixture is prepared immediately before spraying.
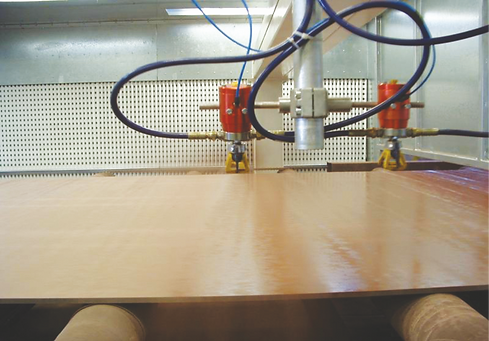
AUTOMATIC SPRAYING
Automatic spraying is used above all to achieve a high production rate. Spraying units based on different technological principles are used for automatic spraying.
Stationary sprayers are used for the treatment of narrow frame edges and flat objects. Objects are fed by a conveyor belt. Photo sensors switch on the sprayers at the moment the object is fed to the spraying area.
Sprayers with horizontal or vertical transversal movements and rotary sprayers are used for the treatment of bigger objects. Contrary to the curtain coaters and the roller units, an automatic spraying unit is capable of treating profiled objects and edges.
Spraying by robotic spray units is used for the treatment of more complicated objects, whereby it is necessary to reproduce the human hand movement. The robotic spray unit consists of a microprocessor and a spraying application. The spraying application is managed by a microprocessor according to the software provided with it.

ROLLER COATING
Roller coating machines are used for treatment of objects with a flat surface. Stains, primers, lacquers and topcoats can be applied with a roller coating machine.
Roller coating machines consist of application and dispenser rollers with doctor-blade rolls and a conveyor belt for the treated objects.

The application roller is covered in a special rubber material. The hardness of the rubber on this roller is indicated by the numbers based on the Shore method.
In accordance with the applied coating, a rubber roller with the appropriate rubber hardness should be chosen: coatings with an organic solvent base = +/- 30 Shore, primers and topcoats- +/- 50 Shore.
The dispenser roller, used to regulate the dosage of the applied material, is made of metal.
The applied quantity can be adjusted by using a) a distance adjustment between the dispenser and the application roller; b) adjustment of the pressure upon the treated object; and c) adjustment of the direction and the rotation speed of the dispenser roller.
Different modifications of roller coating machines are used for treating wooden surfaces.
CURTAIN COATING
The principle of the curtain coater is based upon application of coating by a curtain. The main parts of a curtain coater are: a conveyor belt and coating heads. The material waste is minimised by application of a curtain coater because the over sprayed material is recovered and reused.
Depending on their construction, the curtain coaters may have one or several coating heads. For example, reciprocators with several heads are used for coating with polyester mixtures with a short pot-life.
Thereby one of the applied coatings contains hardener, and another - accelerator. If different materials are to be used in one line, such reciprocators with several coating heads are handy and productive.
There are gravitational and pressure coating heads. Inside the gravitational coating heads the coating passes through the finish blades and forms a coating curtain under the influence of gravity.
Overpressure is used to move the coating material through the finishing blades inside the pressure coating heads. Coating heads can be stationary and removable. The advantage of removable coating heads is that they can be cleaned easily.
If the treated objects are placed at an angle on the conveyor belt, then apart from the surface, the edges can also be treated. Curtain coating allows a high production rate to be reached - the speed of the conveyor belt might be as high as 150 m/min. The material consumption can furthermore be regulated within a wide range (60-450 g/m2).
Different coatings can be applied by a curtain coater, such as nitrocellulose, water-borne, polyurethane, acid-cured and others.


FLOW
COATING
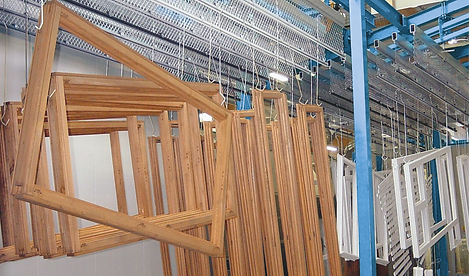
Coating can be applied upon treated objects with the aid of flow. The flows are led upon the objects horizontally or vertically through a stationary pipe system, which moves in single steps under the object. Surplus coating from the objects is led back through recovery channels and is reused later.
It is important to create proper conditions inside the room for the flow coating (low air movement, correct moisture ratio etc) in order to enhance a uniform coating on the object surface and remove surplus stains.
It is also important that the objects are placed on the conveyor belt in a way that allows a good coating flow and minimizes drop forming in sharp corners. A good flow and hiding power are important properties for materials applied by flow coating.
Such materials do not produce any foam while rotating in a system. Furniture and window manufacturers use flow coating mainly for the application of stain, wood impregnators and primers.
The main advantages of flow coating are uniform coating of the surface, small material consumption, low personnel costs and an effective usage of the production site.
TUMBLING
Finishing in a tumbling unit is mainly used for the treatment of small objects. Treated objects are placed inside a cylinder into which an appropriate amount of coating is sprayed.
Then a rotating tumbler is switched on. After the application of the coating, the details are dried by the air blown into the cylinder.