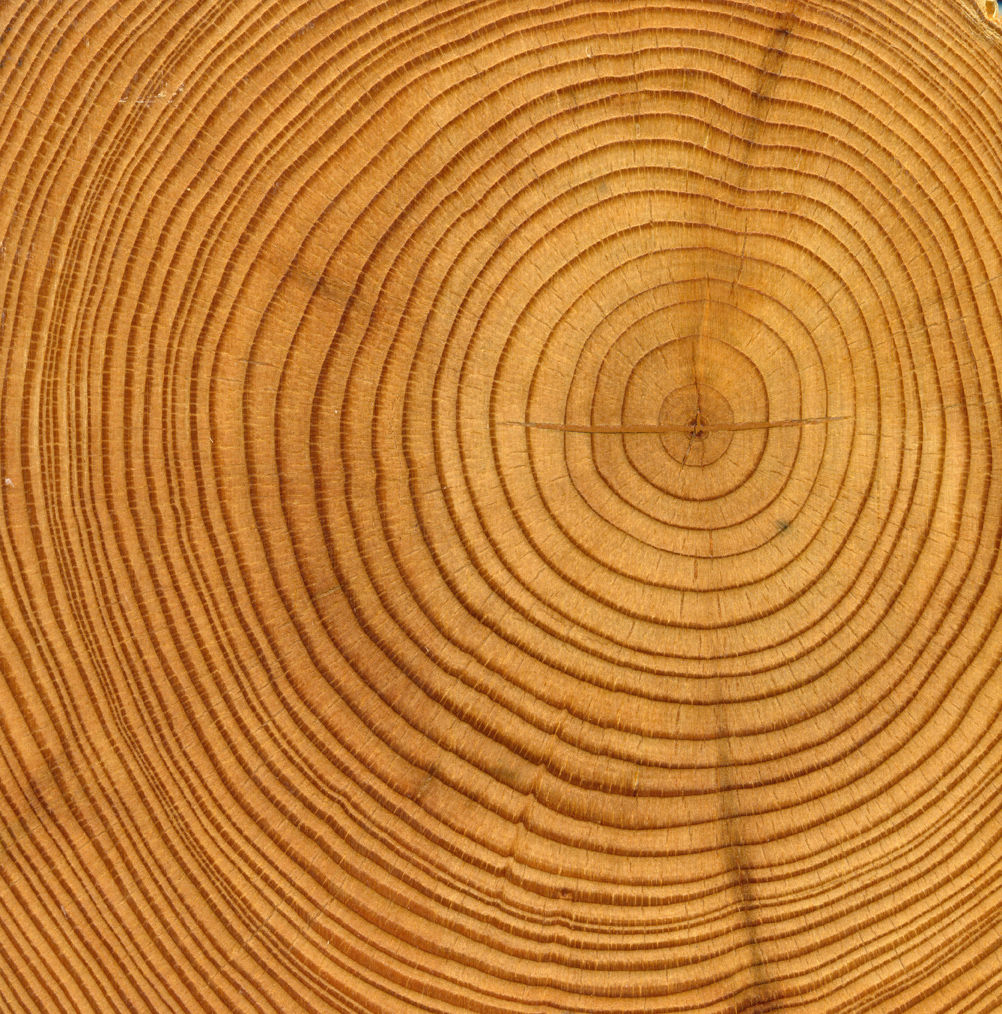

DRYING & CURING
CONVENTIONAL DRYING
Conventional drying is the same as drying at room temperature. This method is widely-used since most industrial coatings start to dry rapidly even at a room temperature.
The drying time depends on the temperature, the moisture and the air exchange.
CHAMBER DRYING
Chamber drying differs from conventional drying by a higher temperature and a more intensive air exchange.
The temperature increase accelerates the solvent evaporation and the chemical reaction, resulting in a reduction of the drying time & an improvement of the applied lacquer or topcoat.
A temperature increase of +10°C can cut down the drying time by 50%. The drying process is extremely intense at a temperature of +50° C.
PHYSICAL DRYING
Some products, such as nitrocellulose ones, dry as a
result of the solvent evaporating. After drying, these materials can be resolved again.
The time for the physical drying is significantly reduced by a temperature increase.
OXIDATION DRYING
The drying and curing of synthetic alkyd resins is caused by the evaporation of solvents and a reaction between the binder and the oxygen of the air.
The drying time of this technique is not influenced very much by any temperature increase.
CHEMICAL CURING
Accelerated curing of an acid-curing material starts as soon as the acid hardener has been added.
Curing of polyurethanes starts after adding the isocyanate-contained hardener.
It is possible to accelerate the solvent evaporation somewhat, and the chemical reaction between the binder and the hardener, by a temperature increase.
DRYING METHODS
Major methods of drying are convection, radiation and pre-heating. These drying methods are often combined.
During pre-heated drying, a pre-heated object transfers part of its temperature to the coating material.
This accelerates the solvent evaporation, and the drying of the coating starts from the object’s surface.
During convectional drying, the object’s surface with the applied coating is dried by circulated air. The drying of the coating starts from the outer surface.
During radiation drying, the coating is dried and cured under the exposure of radiation.
For this drying, UV-radiation (ultraviolet radiation), IR-radiation (infrared radiation) and EB-radiation (electron beam or beta radiation) is used.
DRYING UNITS
Drying units can be different depending on their construction. For an effective usage of the available production space, tunnel or multistage dryers are often used instead of convectional drying.
In case of radiation drying the objects are moved along the conveyor belt at the same angle.
CONVECTIONAL DRYERS
The following stages are required when using convectional dryers: an area for pre-heating, a flash-off area, a drying area and a cooling area.
In the pre-heated area the objects are heated before the coating application. Object pre-heating is used to accelerate the solvent evaporation from the applied coating, as well as to remove the air from the wood pores.
A flash-off is necessary to achieve a good surface treatment quality. In this area most of the solvent evaporates from the coating, which is now uniform along the object’s surface and the remaining bubbles are eliminated.

It is essential to assure a proper air exchange in the flash-off area. A too intensive air exchange can cause disturbances in the remaining bubbles on the surface.
Inside the drying area the temperature is much higher than in the flash-off area. Here the coating drying takes place and the surface gets its basic curing rate. Inside the cooling area the objects are cooled before being removed from the chamber.
The cooling of objects is very important as most coatings are thermoplastic, which means that they soften at high temperatures.
The air exchange inside the cooling area has to be very intensive.
IR-DRYERS (INFRA RED)
The heating power of infra red radiation is used in IR-dryers. Electromagnetic radiation with a wave length of 0,76 μm - 1 mm is called infra red.
Depending on the wave length of the infra red radiation, the following types of IR-dryers can be used: IRS-dryers (infra red short-wave radiation), IRM-dryers (infra red middle-wave radiation) and IRL-dryers (infra red long-wave radiation). IR-dryers are often combined with convectional dryers.
The usage of IR-dryers shortens the coating drying time. The object cooling becomes easier as IR-dryers only heat up the coating.
These dryers are more economical than convectional dryers regarding the power consumption. IR-dryers are also small enough to more effectively use the available production space.
It is also possible to pre-heat objects inside IR-dryers.
Care has to be taken while drying resinous kinds of wood inside IR-dryers, as object overheating may result in an excessive resin release.

UV-DRYERS
Inside UV-dryers the coating is cured under ultraviolet radiation. Lacquers and paints contain an acrylate or polyester based binder = the oligomer, and a sufficient amount of reactive diluents = the monomer, which is used to get the right application viscosity to the UV-curing lacquer/paint.
Under the influence of the UV-light a co-polymerisation starts between the oligomer and the monomer.
Curing occurs very rapidly (10-15 sec for polyesters and 5-8 sec for acrylate).
Two types of radiation sources are used in UV-dryers: “Ga-lamps” and “Hg-lamps.”Ga-lamps” have a wave length >420 nm and a lifetime of approximately 2000 hours.
They are used for curing pigmented primers and coatings and in most cases in combination with “Hg-lamps”. “Hg-lamps” radiate waves of 200-380 nm and have a lifetime of approximately 3000 hours.
These lamps are used for curing of transparent and clear UV-lacquers.
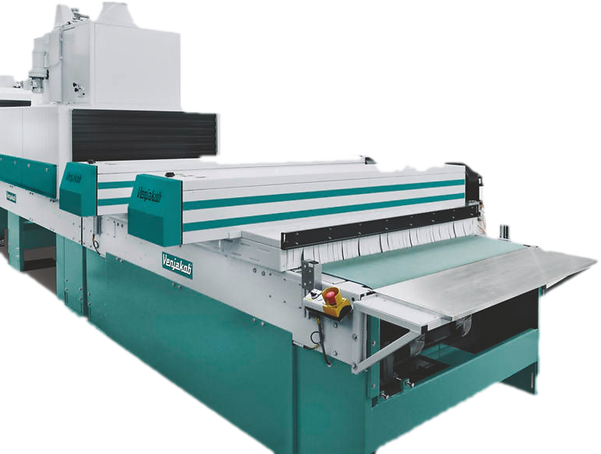
Please note: The UV-lamps need to be checked regularly, using UV-control instruments.
(Checking the UV-energy, the UV-peaks and the peak temperature).
The pre-heating process with object cooling afterwards is not required for UV-dryers.
As curing occurs very fast the length of the finishing line is much shorter.
The energy consumption of UV-dryers is significantly less than that of convectional dryers.
Care should be taken while using stains with over coating with UV-clear coats as the pigment might be solved in the coating and thus slow down the process of curing or even stop it.
Similar problems may occur when treating the different kinds of wood with special resin content.
ELECTRON RADIATION CURING
(EB-curing - dryers with beta-radiation)
The usage of beta-dryers isn’t very common as this technology requires large investments.
An extremely rapid curing process which lasts less than a second is initiated when beta-radiation passes through the coating. Curing is prevented by the oxygen of the air so an inert gas (usually nitrogen) is used to remove the oxygen from the drying area. The usage of beta-radiation allows a high production rate and good quality.
Compared to convectional dryers, the energy costs are 20-50 times less.