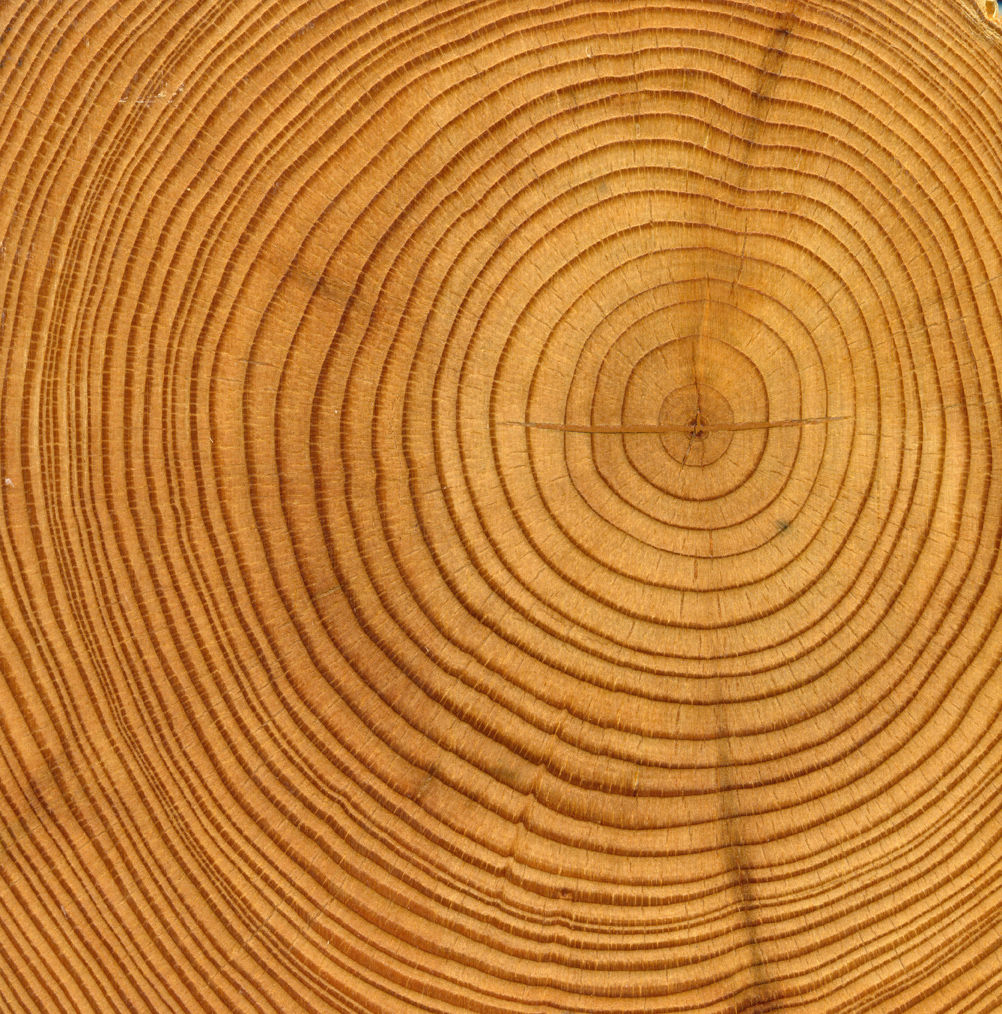
NC-PRODUCTS (NITROCELLULOSE)
NC-products are based on nitrocellulose binders with a large molecular mass usually modified by alkyd binders. The drying of NC-products occurs through evaporation of the solvent. The advantages of NC-products are: short drying time, uncomplicated application and absence of formaldehyde in its contents.
The major disadvantages are: low resistance to chemical and mechanical impacts and a low build coating.
Apart from the ordinary NC-products modified by alkyds, there are products modified by acrylate as well as water-borne NC-products.
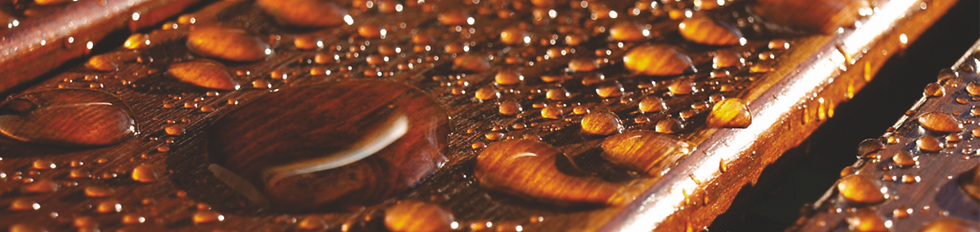
TYPES OF COATINGS
FOR WOOD
WATER-BORNE PRODUCTS
Water (both in total and to a large extent) is used instead of an organic solvent in water-borne materials. Such binders as emulsion, colloidal dispersion or totally water-soluble binders may be used for water-borne products. Considering emulsions, this is a dispersion of a binder, with a large molecular mass, in water.
The main reason for the ever growing usage of water-borne materials is that the emission of organic solvents is avoided or dramatically reduced during the coating process. Apart from that, the water-borne materials have good light and fire resistance.
There are a lot of different water-borne products/technologies with different properties depending on the field of application and demand profile.
The water-borne products can be alkyd-, polyurethane-, acrylate-, or polyesterbased – as one- or two-component products. The water-borne UV-tehcnology is now also used on the market.
The disadvantages of these materials are: storage and transportation can only take place at temperatures above 0, as well as the possible swelling of the wood.
ACID-CURING PRODUCTS
Amino resins (urea or melamine) and alkyd resins, which are often modified with nitrocellulose, are used as binders for acid-cured materials.
Acid-cured materials can have one or two components. An acid hardener should be added to the two-component base before application.
Acid-curing products harden as a result of a polycondensation process which starts when a catalyst (acid hardener) is added. The process of hardening can be dramatically accelerated by increasing the drying temperature and intensifying the air-exchange.
Rapid drying, good hiding power and durability against chemical and mechanical impacts are typical properties of acid-curing materials.
ADDITIVES
Additives are used to achieve special additional properties of the coating products.
Additives are binders, fungicides, defoamers, catalysts, plasticizers, emulgators, anti-skinning agents etc.
POLYURETHANE PRODUCTS
Polyurethane products dry as a result of chemical reactions between the isocyanate and hydroxyl polymer groups. Most PU-products are two-component products based on organic solvents, yet there are also one-component and water-borne PU-products.
Many polyurethane products are modified by acrylate and nitrocellulose. The pot life of two-component polyurethane products is short after adding the hardener, usually 2-6 hours. Compared to the acid-curing products, polyurethanes dry more slowly. PU-products are known for good resistance to chemical and mechanical impacts and have excellent moisture resistance.
Polyurethane coatings developed for exterior use have good mechanical resistance. Thanks to their flexibility they possess good resistance against wood swelling and shrinking which might occur under the influence of weather conditions.
UV-CURING PRODUCTS
UV-curing products are cured by exposure to ultraviolet radiation. Acrylate combined with a photo initiator is often used as a binder. Under UV-radiation the photo initiator starts a rapid process of curing. Apart from the ordinary UV-curing materials which are applied by rolls, there are airless-sprayed UV-lacquers and water-borne UV-products. UV-curing products are acrylate binders or polyester binders, both with a 100% dry-solid content.
The radiation is obtained with UV-curing lamps, of which there are two kinds:
a/ The “Hg-lamp” – cures transparent and clear UV-lacquers;
b/ The “Ga-lamp” – cures pigmented UV-Paints.
Please note: In most cases a combination of “Hg-lamps” and “Ga-lamps” are used for curing primers and topcoats.
In case of water-borne UV-curing products, the UV curing is used at the end of the coating process. The treated object first passes through conventional and/or IRM-drying (medium infra red radiation), which is done in order to evaporate the water, before the final curing can take place.
STAINS
The stain is used to give the wood a different colour, but with a transparency which reveals the structure of the wood. Stains are made up of transparent pigments, binders, water or solvents. The type of pigment used is important in order to achieve the right colour and light resistance of the stain. Lately many water-soluble stains have replaced the solvent-borne qualities.
SOLVENTS
Solvents are used to control the binder’s consistency and are also important for the drying process of the coating. Depending on the type of coating, organic solvents, water or water combined with a small quantity of an organic solvent are used as solvents. The following properties have to be considered while choosing a
solvent: rate of evaporation, electrical conductivity, flash point and dissolving capability.
Evaporation is the ability of a liquid solvent to evaporate. Hereby the solvents can be theoretically divided into three groups: rapid, medium and slow. Slow solvents prolong the drying time of a coating improving its flow so that the surface becomes smoother and glossier. The usage of rapid solvents allows the drying time to be reduced. Yet some condensed moisture can remain under the applied coat of lacquer which may result in the appearance of white spots. Apart from the above mentioned aspects, the application method and weather conditions determine the choice of the correct solvent.
Conductivity depends on solvent polarity: polar solvents are good electrical conductors and the opposite. A correct mixture of solvent components must be chosen in order to attain the required conductivity for the process of electrostatic application.
Flash point is the temperature at which vapours of the solvent when mixed with oxygen can be ignited by a spark or open fire.
Most of the paint- and lacquers for industrial use contain several types of organic solvents. The choice of solvent and its mixture depends upon the requirements of the final product. The most common organic solvents for coatings are: alcohols, acetates, ketones, aromatic mixtures etc.
Alcohols are widely-used polar and photochemical non-active solvents. Alcohols cannot be used in two-component polyurethane products because the OH-alcohol group causes an active reaction with the NCO-group of the polyurethane.
Acetates are widely-used for both acid-cured, nitrocellulose and polyurethane products. Depending on the evaporation speed, acetates can be divided into rapid ones (Methyl Acetate) and medium ones (Butyl Acetate). Acetates are not photo/chemically reactive.
Ketones offer a very strong solvency which is important for reducing the coating viscosity, and they are good electrical conductors. The most popular keton is acetone, which has a very high speed of evaporation and a low flash point, making it extremely flammable.
Aromatic solvents are present in acid-curing, polyurethane and NC products. All aromatic solvents are photo/chemically reactive. The most widely-used aromatic solvents in coatings are toluene and xylene.